두꺼운 원장에 접히는 부분만 음각 패터닝
원가 낮추지만 빛 산란⋅굴절 제어 관건
삼성전자가 폴더블 OLED(유기발광다이오드) 커버윈도로 쓰이는 UTG(초박막유리) 수율 및 단가 문제를 해결할 새로운 기술 개발에 돌입했다. 삼성전자는 OLED에 UTG가 붙어 있는 폴더블 OLED 모듈을 삼성디스플레이로부터 통으로 구매하지만, 물량 중 일부는 OLED만 사서 베트남 내작 라인에서 자체 생산한 UTG를 붙여 쓴다.
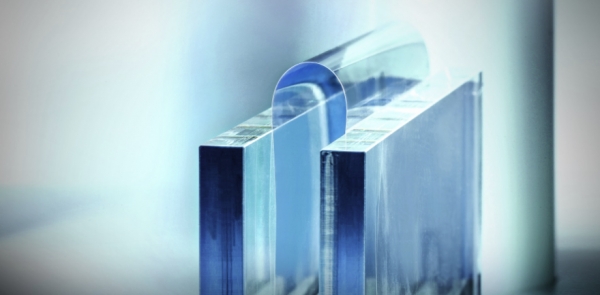
31일 디스플레이 장비 업계에 따르면 삼성전자는 기존 UTG 보다 두꺼운 유리 원장을 사서 폴딩되는 부분만 레이저로 깎아내는 기술을 개발하고 있다. 이를 위해 베트남 스마트폰 소재⋅부품 자체 생산라인에 레이저 패터닝 설비를 한 대 도입했다. 이 설비는 레이저 장비 전문업체인 필옵틱스가 공급했다.
현재 삼성디스플레이가 폴더블 OLED에 사용하는 UTG 두께는 30µm(마이크로미터)다. 워낙 두께가 얇아 가공하기 어렵기 때문에 10장을 접착제로 붙인 뒤 필요한 크기로 자르고, 다시 낱장으로 떼어 낸다.
UTG 원장을 톱날이나 레이저로 자르는 과정이나, 접착제로 붙이고 다시 낱장으로 떼어내는 공정에서 대규모 불량 발생이 불가피하다. 이는 UTG 생산 원가를 높이는 원인으로 지목됐다. 최근 폴더블용 UTG 한 장 가격이 1만5000원선으로 내려온 것으로 추정되지만, 지난해까지만 해도 4만원 안팎에 거래됐다.
이에 삼성전자는 UTG 가격을 떨어뜨리기 위해 지난해 봄 UTG 내재화 프로젝트를 가동했고, 올해 출시된 ‘갤럭시Z 플립3’용 UTG 일부를 자체 조달했다. 삼성디스플레이에서 폴더블 OLED만 사다가 자체 생산한 UTG를 합착해 쓴 것이다.
삼성전자는 이에 그치지 않고, 삼성디스플레이와는 전혀 다른 접근 방식으로 UTG를 생산하는 방안을 연구 중이다. 삼성디스플레이가 처음부터 30µm의 얇은 원장을 이용해 가공하는 것과 달리, 삼성전자는 두꺼운 원장의 접히는 부분만 레이저로 깎아내는 방법을 개발하고 있다.
삼성전자가 개발하는 기술은 성공만 한다면 생산 원가를 낮추고, 수율을 높이는 데 결정적 역할을 할 것으로 기대된다.
UTG 생산에 쓰이는 30µm 원장 유리는 독일 쇼트가 독점 생산하는 탓에 원장 자체가 비싸다. 쇼트는 30μm 외에 50μm⋅70μm⋅100μm 두께 원장도 판매하는데, 한 단계 두꺼워질 때 마다 약 30%씩 가격이 낮아지는 것으로 알려졌다.
어차피 폴더블 스마트폰에서 접히는 부위는 패널 정 중앙 한줄 밖에 없으므로, UTG 전체가 30µm일 필요는 없다는 게 삼성전자의 시각이다. 레이저를 이용해 두꺼운 원장 가운데 부분을 음각 형태로 파내면 인폴딩 방식으로 쉽게 접힌다는 것이다.
이는 삼성디스플레이가 내부 힌지(SUS 프레임 or CFRP)에 유연성을 확보하기 위해 사용하는 방법이기도 하다.
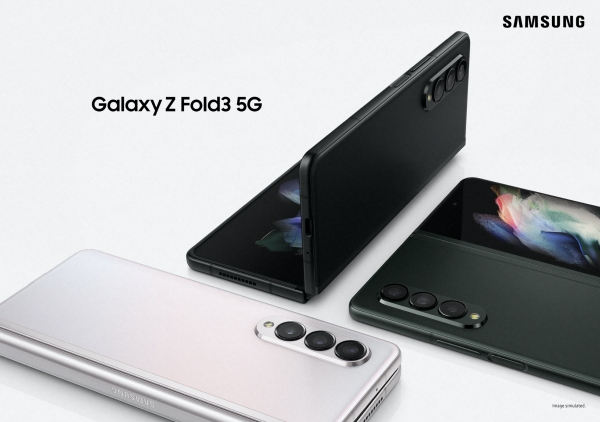
관건은 음각으로 레이저 패터닝한 부분에서 일어나는 빛의 산란이나 굴절을 어떻게 제어하느냐다. UTG는 OLED 화면 위를 덮고 있기 때문에 디스플레이 빛을 왜곡 없이 투명하게 통과시켜야 한다. 그러나 레이저로 유리 표면을 깎아내면 거친 표면 탓에 빛의 산란⋅굴절에 따른 왜곡이 일어날 수 있다. 이에 삼성전자는 레이저로 깎아낸 표면을 채울 레진까지 같이 개발하고 있다.
유리와 굴절률이 동일한 투명 레진을 깎여진 부분에 채워넣고 굳히면 빛의 왜곡은 없애면서 유연성은 유지할 수 있을 것으로 본다. 한 디스플레이 소재⋅부품업체 관계자는 “삼성전자는 폴더블 스마트폰 단가를 떨어뜨리기 위해 내부에 사용하는 소재⋅부품을 이원화하고, 일부는 내작을 강화하는 방식을 쓰고 있다”며 “특히 가격이 비싼 UTG가 단가 인하 1순위”라고 말했다.