최대 12개 챔버를 1개 시스템으로 구성
플랫폼 차원에서 에너지 35% 감축
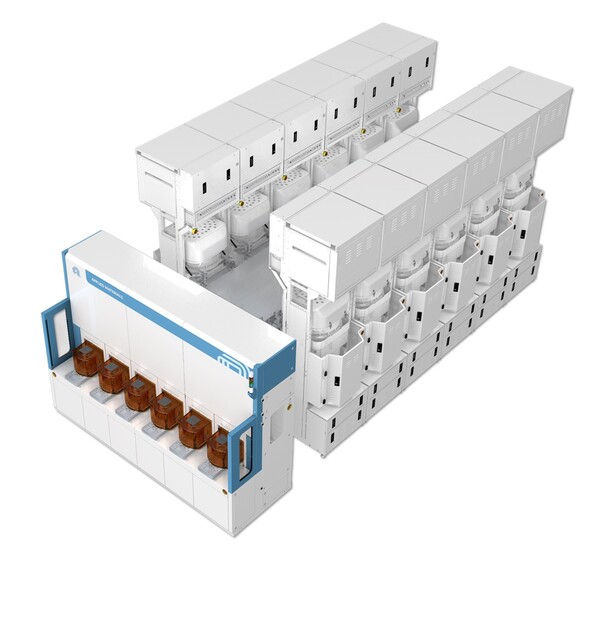
“비스타라 플랫폼을 도입하면 반도체 공장 내 필요 면적을 30% 절감할 수 있습니다. 이는 장기적으로 팹 운용 비용을 절감할 수 있게 해줍니다.”
미국 반도체 장비 제조사 어플라이드머티어리얼즈(이하 어플라이드)는 30일 경기도 성남에 위치한 한국법인에서 기자간담회를 열고, 다섯번째 플랫폼 ‘비스타라’를 공개했다. 플랫폼은 여러개 챔버를 묶어 다양한 공정을 한번에 처리할 수 있는 설비다. 통상 증착⋅식각⋅계측 등의 공정이 개별 장비에서 이뤄지는 게 보통이지만, 플랫폼을 이용하면 여러 공정을 한 번에 처리할 수 있다. 플랫폼을 ‘반도체 공장 안의 공장’이라고 부르는 이유다.
어플라이드는 지난 1990년 엔듀라를 시작으로 센튜라⋅프로듀서⋅센트리스 등의 플랫폼을 출시했다. 이번에 공개한 플랫폼 비스타라는 2010년 이후 13년만에 내놓은 다섯번째 플랫폼이다.
비스트라가 기존 플랫폼 대비 가장 크게 달라진 점은 최대로 구성할 수 있는 챔버 수다. 종전 센트리스까지는 최대 6개 챔버까지 구성할 수 있었지만, 비스타라는 12개 챔버까지 넣을 수 있다. 고객사가 총 12개 챔버가 필요한 경우, 원래는 센트리스 2개 시스템으로 6개 챔버씩 붙여야 했다. 비스타라는 12개 챔버를 한데 붙여 1개 시스템으로 만들 수 있다.
챔버 크기는 소형⋅중형⋅대형 모두 적용 적용할 수 있고, 최다 7개 공정을 지원한다.
이처럼 시스템을 단일화하면 공통으로 쓰는 이송부 공간, 열교환기, 냉각기 등을 줄일 수 있다. 배관이 들어가는 공간과 관리 포인트도 절감할 수 있다. 장대현 어플라이드 메모리 식각기술 총괄은 “비스타라 플랫폼을 도입하면 플랫폼 차원에서 최대 35%, 시스템 차원에서 최대 10% 에너지 소모를 줄일 수 있다”고 말했다.
이 같은 플랫폼 방식 생산은 미세 공정이 발전할수록 필요성이 커지고 있다. 기존에는 단일 시스템에서 하나의 공정만 진행해야 효율성이 높았다. 그러나 공정 변경을 위해 시스템과 시스템 사이를 옮겨다니면 필연적으로 진공이 깨질 수 밖에 없다. 이 과정에서 이물이 혼입돼 웨이퍼 불량률이 높아질 수 있다. 미세공정이 발전할수록 플랫폼 방식 생산이 요구되는 이유다.
어플라이드는 비스타라 플랫폼에 자체 공정챔버 외에 타사, 나아가 경쟁사 챔버까지 믹스할 수 있게 지원할 계획이다. 다만 이들 챔버를 한번에 컨트롤하는 통합 소프트웨어는 어플라이드가 직접 개발하기에 단기에 경쟁사 챔버까지 믹스하기는 쉽지 않을 전망이다.
장 총괄은 “현재 국내외 메모리 회사에 비스타라가 쉬핑(반입)돼 검증을 진행하고 있다”며 “로직 반도체 제조사에도 곧 반입될 것”이라고 말했다.