The biggest loser of the price free-fall was Sapphire Technology, the world’s largest sapphire ingot maker, which has spearheaded WPM Super Sapphire Single Crystal Material Project Group, a government-sponsored development consortium.
In the first quarter of fiscal 2012 ended on March 31, Sapphire Technology was operating its production line half at its capacity, racking up an operating loss of 2.6 billion won on revenues of 4.8 billion won.
Looking forward, however, the sapphire ingot maker will likely turn around in the second half of 2012, or beyond, as there are signs that demand for LED chips will bounce back in 2013.
The company is reported to sign up a 30 billion long-term supply contract.
The comeback of Sapphire Technology on solid footing bodes well for the consortium’s long-term future.
Sapphire substrate is a key base material for growing epitaxial layers and etching blue and white LED chips. Back in September 2010 when the 16-member consortium was formed, the country still depended on imports of sapphire ingot for the largest chunk of LED chip production.
This was despite Korea was then one of the worlds’ largest producer of LED chips, with Samsung, LG Innotek, Seoul Semiconductor Co., Ltd operating about 3000 MOCVD tools, a machine that deposit several layers of gases to etch LED chips on sapphire substrates.
To reverse the highly tilted supply chain against Korean LED chip and module makers alike, the Korean government pinpointed sapphire ingot as one of the country’s 10 strategically important base materials for the country’s IT industry under.
Part of the government’s WPM, or world 10 premier materials project, which is aimed at bringing the country’s base material industry to world top-class level, the super sapphire development consortium has succeeded in commercializing 6-inch sapphire ingots in 2011.
By 2015, the consortium aims to start mass-production of 8-inch sapphire ingots.
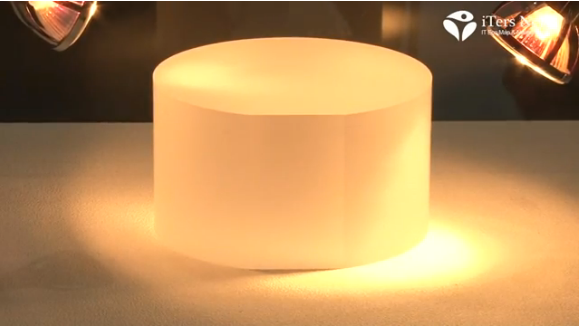
The localization drive of sapphire ingots is not only aimed at substituting imports, but also targets to remake the country as one of the world’s largest export country of sapphire ingots as well a substrates.
According to the consortium, Korea is expected to make up 35% share of worldwide sapphire ingot market and 20% share of global sapphire substrate market by 2015.
Seong-min, Hong, staff with the consortium’s research center, a 6-inch sapphire wafer substrate can generate more than two times the productivity than a 4–inch allowing LED chip makers to churn out 17,370 LED chips per wafer.
The 8-inch sapphire wafer also can enable chip makers to roll out two thirds more productivity, or 31,380 chips per wafer.
The gains in productivity will help LED chip makers to drive down costs dramatically, which will in turn fuel demand for LED lighting solutions, making them an affordable alternative to fluorescent bulbs and tubes.
According to Hong, to make a sapphire ingot requires C-axis and A-axis growing of alumina, base material. Then, ingot makers use ultra thin diamond thread to slice the ingot into myriad layers of ultra-thin substrate disk.
The 16-member consortium group includes Sapphire Technology, Korea Research Institute of Standard and Science, Kusan National University, Korea Institute of Industrial Technology, KCC, KC, Cristech, Korea Institute of Ceramic Engineering & Technology, Hansol Technics, Iljin Display, Iljin Diamond, Ehwa Diamond Industrial Tool, Seoul Semiconductor, Korea Institute of Industrial Technology, Seoul National University, Korea Polytechnic University.